6 Sigma Tools for the Best Six Sigma Black Belts (Learn 6Σ)
To ensure quality improvement, the best six sigma black belts use the different 6 sigma tools. These Six Sigma tools are written in two ways. Such as 6Σ or 6σ or SS. However, there is described the quality control, principles, and 6 useful tools.
Quality Control of 6 Sigma Tools:
A company can use Six Sigma as a quality management tool to improve proficiency in its strategy implementation. The 6Σ aims at producing not more than 3.4 defects per million of parts produced in the manufacturing process. It uses a variety of statistics to determine the best practices for any given process.
Statisticians and SS consultants study the existing process and determine the methods that produce the best overall results. It statistically ensures that 99.9997% of all products created in a process are acceptable quality; it allows only 3.4 defects per million opportunities. If a given process fails to meet this criterion, it re-analyzes alters and tests to determine any improvements. Suppose no development finds, the procedure re-examins, changes, and tests again. This cycle repeats until an improvement becomes visible. Once an improvement is found, it’s documented. The knowledge is spread across other company units to implement this new process and reduce their defects per million opportunities.
SS experts are known as Green Belts and Black Belts. They evaluate the business process and determine ways to improve the existing process. They can also design a brand new business process using DFSS (Design for 6σ) principles. Typically it is easier to define a new process with DFSS principles than refining an existing process to reduce the defects.
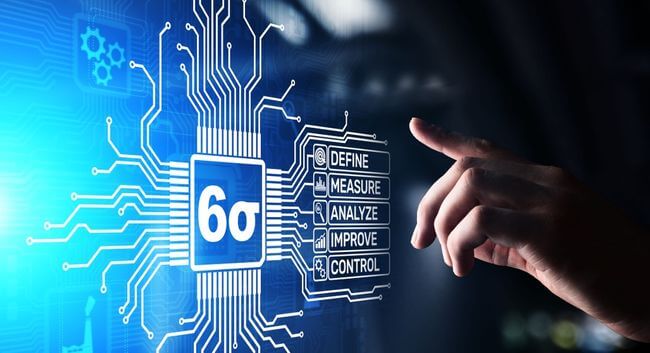
Use of 6Σ or Six Sigma Principles:
Its methodology advances any existing business procedure by constantly revising and re-tuning the process. To attain this, it uses a methodology known as DMAIC. DMAIC contains five different meanings. Such as:-
- D = Define opportunities
- M = Measure performance
- A = Analyze opportunity
- I = Improve performance, and
- C = Control performance
Even though it was initially applied at Motorola to develop the manufacturing procedure, all businesses can profit from implementing Six Sigma. The 6Σ methodologies use in many Business Process Management (BPM) initiatives these days. These BPM initiatives do not necessarily relate to manufacturing many of the BPMs that use 6 Sigma in today’s world include call centers, customer support, supply chain management, and project management.
Businesses in various industry segments such as the services industry (example: Call Centers, Insurance, Financial or Investment Services), e-commerce industry (example: B2B/ B2C websites), and education can use Six Sigma principles to achieve higher quality. Many big businesses such as General Electric, Sony, Ford Motors, Nokia, Texas Instruments, Hitachi, Toshiba, Canon, DuPont, American Express, Polaroid, and Motorola have successfully implemented SS. Still, the adaptation by smaller businesses has been prolonged.
Different Names of it:
SS improves profitability through improving quality and efficiency. Evidence shows that many companies that implemented 6σ have seen profit margins grow 20% year after year for each sigma shift (up to 4.8 to 5 sigma). Six Sigma allows top leaders in organizations to be proactive, rather than reactive, to quality issues; Reactiveness emerges from the fact that SS focuses on the process that creates or eliminates the defects rather than on the mistakes themselves.
Tools used by Six Sigma Black Belts:
There are described several tools which mostly used in the project by six sigma black belts. Such as:
- Quality Function Deployment (QFD)
- Causes and Effect Matrix (C&E Matrix)
- Failure Mode and Effect Analysis (FMEA)
- T-Test
- Control Charts
- Design of Experiment (DOE)
1. Quality Function Deployment (QFD):
Firstly, QFD supports Six Sigma Black Belts’ drive consumer-focused improvement across the strategy procedure. QFD is a system. It consists of a set of methods to identify, communicate, and prioritize customer requirements. With QFD, 6 Sigma groups can more efficiently focus on the actions that mean the most to the consumer, beat the opposition, and align with the organization’s task.
2. Causes and Effect Matrix (C&E Matrix):
The C&E Matrix helps SS project leaders facilitate the team’s decision-making. The Causes and Effect Matrix is a tool. It helps Six Sigma squads to prioritize, analyze, and select the data. They accumulate throughout a scheme to recognize glitches in that procedure. The 6Σ teams usually use the Causes and Effect Matrix in the Measure phase of the DMAIC method.
3. Failure Mode and Effect Analysis (FMEA):
FMEA assistances SS teams to detect and address faults in a product or procedure before they happen. Before applying new processes, services, or products, Six Sigma teams use FMEA to isolate techniques. An effective FMEA identifies corrective actions required to prevent failures from reaching the customer and improve performance, quality, and reliability.
4. T-Test:
Using small sample sizes, the t-test ensures the six sigma teams validate the result. Determining the statistical differences or similarities between two group, it has a significant contribution. It doesn’t give just a difference due to random chance. SS teams might use it to determine if a plan for a comparative analysis of patient blood pressures before and after they receive a drug is likely to provide reliable results.
5. Control Charts:
For assessing the process stability, the control chart is beneficial for SS. Control Charts are a simple but extremely actual tool for improving and monitoring process enactment over time. Because they aid Six Sigma teams to see and scrutinized disparity. The three elementary mechanisms of any control chart are upper, centerline, and lower statistically strong-minded control restrictions, and performance data conspired over time.
6. Design of Experiment (DOE):
Finally, DOE helps Six Sigma Black Belts create the most cherished assets. DOE is a statistical method that embraces the design, planning, data collection, interpretation, and analysis strategy used by 6σ professionals. 6 Sigma teams practice DOE to define the liaison between factors (Xs) affecting a procedure and the output of that procedure (Y).
Six sigma is a set of tools and techniques for the improvement process. It is very important for those people who are related to business and entrepreneurs. Thank you so much for sharing this nice article with us.
With thanks for sharing your superb website!