Total Quality Management (TQM)
Before understanding the meaning of Total Quality Management (TQM), let us first know what does Quality means? Quality is a parameter that decides the inferiority or superiority of a service or product. Quality plays an important role in every business. Business marketers got to emphasize the standard of their brands over quantity to survive the cut-throat competition. However, there are discussed the aspects, characteristics, principles, framework, importance, merits, and demerits of TQM.
What is Total Quality Management (TQM)?
Total Quality Management is a management approach. It builds with three different things, for example, system, method, and purpose. Firstly, the system includes all persons of all divisions at every level. Secondly, the method runs itself with the management method and analytical method. Thirdly, purpose absorbs the quality, cost, environment, delivery, and safety.
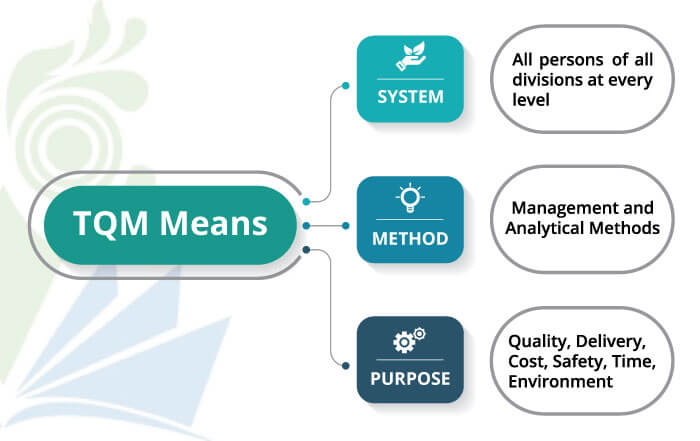
TQM is the short form of Total Quality Management. It is a continuous process by the management and employees of a specific organization to make sure future customer satisfaction and customer loyalty. In other words, one satisfied and happy customer indeed brings ten new customers along with him. In comparison, one unsatisfied customer will spread bad word of mouth and harm the existing environment and potential customers.
Total Quality Management (TQM) is a management approach that is ensured long-term success through customer satisfaction.
Therefore, total quality management (TQM) is the act of managing the whole to achieve excellence. TQM is a strategic management model in the field of administration, management, as well as governance. Similarly, TQM is one of the modern public administration paradigms.
3 Aspects of Total Quality Management:
After that, reaching the various author’s writing, we can explore TQM’s three specific aspects. In other words, its name is 3Cs of total quality management. Such as:-
- Counting: 3Ts (Tools, Techniques, and Training) used to analyze, understand, and solve quality problems.
- Customers: Quality is a central concern and driving force for a customer.
- Culture: Expressed beliefs and shared values of leaders support and define the quality.
Characteristics of Total Quality Management:
There are mentioned some very important characteristics of total quality management. For instance:-
- Proper communicating and adopting TQM.
- Benchmarking or evaluating by comparison with a standard.
- Closer customer relation environment.
- Increased training facilities for workers or employees.
- Closer provider relation situation.
- Ensuring employee empowerment.
- Process measuring
- Open organization
- Process improvement
- Flexible production
Elements & 6Cs of TQM
Elements are the core thing of any concept. Without a specific element, a concept can’t build properly. Trust, integrity, training, teamwork, leadership, recognition, communication, etc. are TQM elements.
If a business or organization wants to implement total quality management in its environment, some factors have to ensure. These important factors are called 6Cs togetherly. Such as:
- Commitment
- Culture
- Continuous improvement
- Cooperation
- Customer focus
- Control.
Structure of TQM:
The structure of total quality management is a continual improvement concept. It integrates the staff, customers, and suppliers of a business or organization. Moreover, it maintains the quality of work, process, and enterprise results. As a result, TQM constitutes the quality of leadership, learnability, and show consistency.
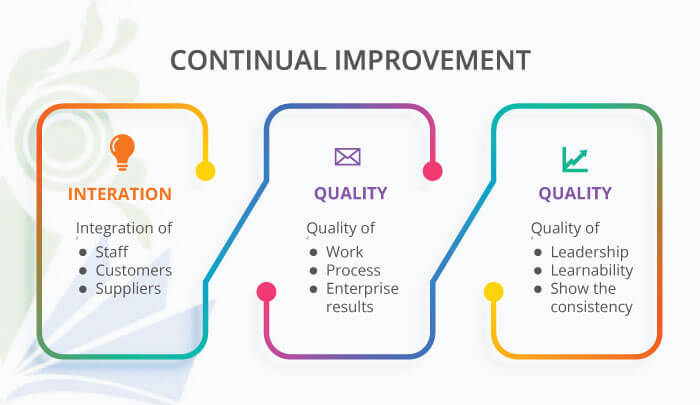
Principles of Total Quality Management:
Total Quality Management (TQM) has five principles. Such as:-
- Management Commitment
- Focus on Customer and Employee or Employee Empowerment
- Focus on Fact
- Continuous Improvement
- Everybody Participation
The Concept of Continuous Improvement by TQM:
Total Quality Management mostly cares for continuous improvement in decision-making, from the high-level strategic plans to detailed rub out of work things on the shop floor. TQM stocks from the belief that falses step can avoid and defects can prevent. It plays to continuously developing results, in all perspectives of work, due to constantly improving machine capabilities, people, technology, and processes capabilities.
However, it must deal not only with developing results but more significantly with developing capabilities to create better results in the coming times. There are five finest areas of focus for ability development: supply generation, demand generation, operations, technology, and people capability.
The main principle of TQM is that people may make mistakes, but most of them cause, or at least allowed, by faulty processes and systems. This denotes that the root cause of such mistakes can be eliminated, repeated, and identified. It can protect by changing the procedure. That is to say, here has three vital mechanisms. Such as:-
- Firstly, preventing mistakes from occurring.
- Secondly, mistakes can’t be perfectly prevented, making them out early to protect them from being passed down the value-added chain.
- Thirdly, where mistakes return, put a stop to produce until the procedure can be accurate. Besides, it is to protect the production of more problems.
The framework of Total Quality Management:
Here includes a framework of total quality management. For example:-
- Point out the degree of commitment, list down and key interest the long-term changes required.
- Define the objectives of total quality management.
- Identify resources available and develop an understanding of the organizational system with the quality system.
- Detect top management commitment through quality processes, procedures, and policies.
- Create a participative work environment
- Design plans
- Develop strategies for implementing
- Allocate resources
- Implement & monitor
- Measure benefits in terms of increased customer satisfaction
- Review and reward
Importance of Total Quality Management:
Quality management ensures superior quality services and products. The quality of a service or product can measure in terms of durability, reliability, and performance. It is a sensitive standard that converts an organization from its opponent. Quality management tools ensure changes in the processes and systems, resulting in superior quality services and products. The methods of quality management, such as Six Sigma or Total Quality management. These have a common goal – to deliver a high-quality product. Customers need to satisfy with your brand. Business marketers are successful only when they emphasize quality rather than quantity. Quality products or services ensure that you survive the cut-throat competition with a smile.
Therefore, total quality management implements close coordination between employers and employees in an organization. It fixes a strong feeling of teamwork in the employees.
Guru of Total Quality Management:
- PDCA (Plan, Do, Study & Act) or (Plan, Do, Study & Adjust)
- OPDCA (Observe the current condition, Plan, Do, Study & Act)
- KAIZEN (KAI=Change & ZEN=Improvement)
- Six Sigma
- Deming’s 14 Points on Quality Management
- Atarimae Hinshitsu
- Kansei
- Miryokuteki Hinshitsu
Benefits of TQM:
There are mentioned some important benefits of total quality management. Such as:-
- Employee participation in the decision-making process.
- Improved quality of service or product.
- Developed in teamwork span or steps.
- Ensured customer satisfaction from the client.
- Strengthen the working relationships between employee and employer or employee and employee.
- Ensured employee satisfaction in the working environment.
- Increased productivity with quality maintenance.
- Creating good communication through scientific techniques.
- Getting profitability in business.
- Shifting market share positively.
Drawbacks of TQM:
There are issued some important drawbacks of total quality management. For instance:-
- Extremely demanding of management and staff time.
- It can become excessively mechanical and bureaucratic and lead to prominence on the process’s stability, rather than a focus on improvement or the means rather than the end.
- Only help if the organization is heading in the right direction.
- It is not a quick fix. Total quality management takes years to implement.
- It can lead to too much attention.
In conclusion, Total Quality Management (TQM) motivates contribution among the floor managers and workers. There is no single theoretical establishment of total quality, but Juran, Ishikawa, Deming, etc. layout the core premise.
Like!! Great article post. Really thank you! Really Cool.
Thank you for your post.
It’s going to be end of mine day, but before finish I am reading this great post to increase my knowledge.
It’s remarkable to pay a visit this web site and reading the views of all friends about this paragraph, while I am also keen of getting knowledge.
Hi there, just wanted to tell you, I enjoyed this post. It was inspiring. Keep on posting!